Articles
Follow our developments and deepen your industry knowledge by following our updates and news.
Cryogenic infrastructure at API facility
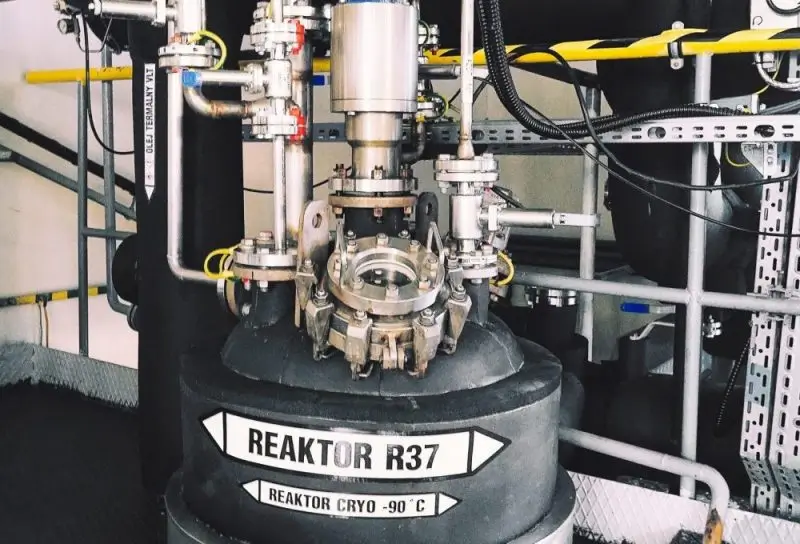
Polpharma is able to meet new challenges thanks to the competences of its employees in cryogenic and the possibility of gradual scaling up of processes (from 1 liter in laboratory scale to 6000 liters in technical scale).
Cold manufacturing
Cryochemistry is the study of chemical interactions at temperatures below −150 °C (−238 °F; 123 K). It is derived from the Greek word cryos, meaning 'cold'. But in traditional API manufacturing, cryochemistry refers to the temperatures of about -80°C.
Cryogenic conditions facilitate precise chemical transformations that require very low temperatures. Reactions carried out under such conditions allow to:
- reduce impurities,
- minimize undesirable side reactions and
- control the volatility of products to ensure complete safety of the process until the end of the transformation.
Running reactions at very low temperature can provide higher yield and purity (e.g. of desired isomers). Low temperature is also used to control the reactivity of exothermic processes.
New drug molecule candidates appearing on the market are increasingly complex. And greater complexity usually means more difficult syntheses and the need for organic transformations that proceed with exceptional selectivity: stereoselectivity, regioselectivity and chemoselectivity.
This are some examples of reactions widely used in pharmaceutical synthesis, run at low temperatures:
- metal-organic reactions(e.g. lithiations, Suzuki couplings)
- chlorinations,
- alkylations,
- reductions,
- asymmetric reactions (e.g. Michael additions)
- Friedel-Crafts.
New infrastructure at our facility
Polpharma has invested in the appropriate infrastructure and now we are able to conduct the processes up to (-80)0C on a laboratory and pilot scale. This enables us to deal with highly reactive compounds while improving the selectivity of the reaction on a laboratory (1 liter scale), kilo lab (25 liters scale), pilot (135 liters, 400 liters) currently and manufacturing scale (2500 liters, 6000 liters) in the coming future (first half of 2024).
Low-temperature reactions require special equipment.
Our new infrastructure does not only consist of properly designed reactors, made of the right material, but also auxiliary equipment such as condensers, heat exchangers, pumps, etc.
Scale-up capabilities
Speaking of cryogenic capabilities, the challenge is not only to have the right, expensive equipment, but also the issues associated with scaling up of such processes.
Polpharma is able to meet these challenges thanks to the competences of its employees and the possibility of gradual scaling up of processes (from 1 liter in laboratory scale to 6000 liters in technical scale).
Author
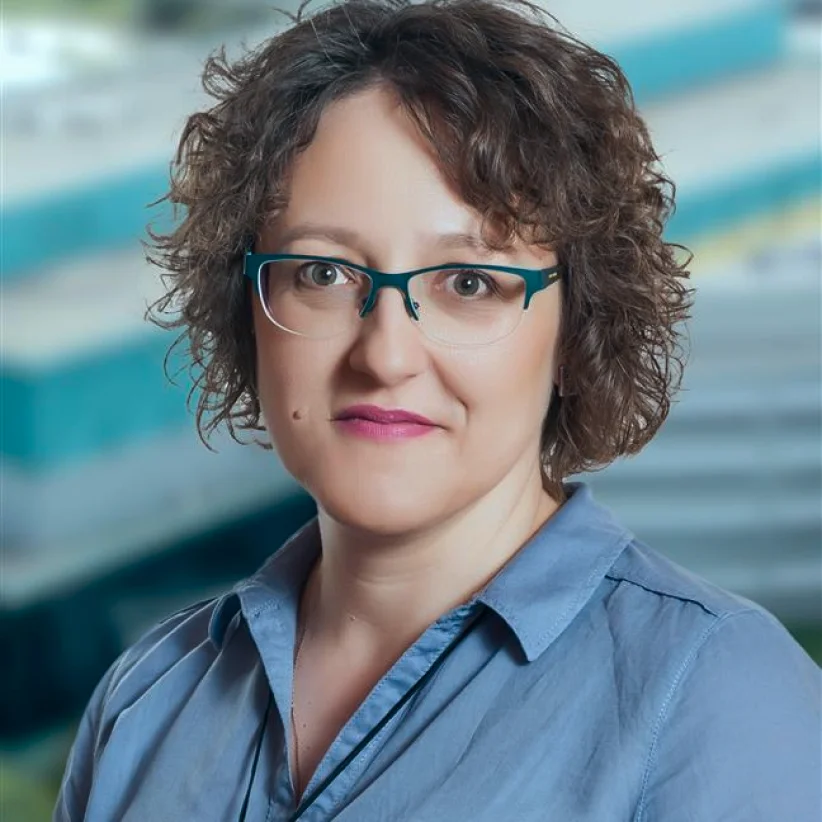
Advisor for Technical Support for Business Development and CDMO